Abstract High-performance coated tools have become the symbol of modern cutting tools. At present, the proportion of coated tools in developed countries has exceeded 80%, and the tool coating technology has become one of the key factors to improve the technical level of manufacturing. . Metal nitride hard coating has a high...
High-performance coated tools have become the symbol of modern tools. At present, the proportion of coated tools in developed countries has exceeded 80%, and the tool coating technology has become one of the key factors to improve the technical level of manufacturing. The metal nitride hard coating has high hardness and wear resistance, which can effectively reduce various mechanical wear, chemical corrosion and high temperature oxidation, so that the life of the coating tool is significantly improved.
AlCrN coating is one of the excellent nitride coatings. Compared with the CrN coating, the ternary Cr–Al–N coating formed by adding Al has greatly improved the performance of anti-abrasive wear and high-temperature oxidation. The AlCrN coating formed by adding Al has high hardness and Good characteristics such as chip removal mechanism, so it shows excellent friction and wear characteristics under high load conditions, and the coating load bearing capacity is obviously improved, which greatly broadens the service range of Cr-based PVD hard coating; compared with AlTiN Coating, because Cr has a higher melting point than Ti, the AlCrN coating with Cr instead of Ti can significantly improve the high temperature oxidation temperature, the friction coefficient is smaller, the chip removal ability is stronger, the adhesion resistance is better, and the toughness is better. It is more suitable for interrupted cutting. Although the hardness is slightly reduced, the overall performance is better. AlCrN coating is also the most typical representative of current PVD nitride coating.
AlCrN coating is one of the excellent nitride coatings. Compared with the CrN coating, the ternary Cr–Al–N coating formed by adding Al has greatly improved the performance of anti-abrasive wear and high-temperature oxidation. The AlCrN coating formed by adding Al has high hardness and Good characteristics such as chip removal mechanism, so it shows excellent friction and wear characteristics under high load conditions, and the coating load bearing capacity is obviously improved, which greatly broadens the service range of Cr-based PVD hard coating; compared with AlTiN Coating, because Cr has a higher melting point than Ti, the AlCrN coating with Cr instead of Ti can significantly improve the high temperature oxidation temperature, the friction coefficient is smaller, the chip removal ability is stronger, the adhesion resistance is better, and the toughness is better. It is more suitable for interrupted cutting. Although the hardness is slightly reduced, the overall performance is better. AlCrN coating is also the most typical representative of current PVD nitride coating.
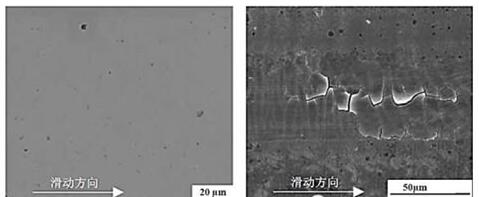
Left: AlCrN coating Right: CrN coating
For the current manufacturing industry that advocates high-speed cutting and hard cutting, it is necessary to develop a new coating that can maintain high hardness, high wear resistance and high temperature oxidation resistance under high-speed cutting conditions. The AlCrN coating maintains a hardness of 27 GPa at 1000 °C, which is the optimum hardness of the nitride at this temperature.
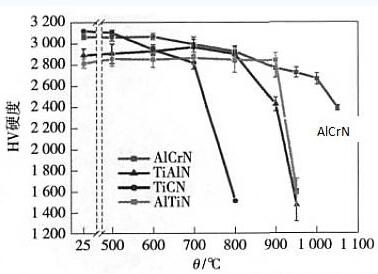
Red hard contrast
Cr element is the main element to improve the hot corrosion resistance. Al element can promote the formation of stable Al2O3 film, so A lCrN coating has good anti-corrosion performance and high temperature oxidation resistance. Compared with other coatings, AlCrN coatings are widely used in cutting, bearings, and bearings due to their high hardness, good wear resistance, high temperature oxidation resistance and excellent red hardness under 1100 conditions. Stamping, aluminum die casting, high temperature alloy processing, wear parts and other fields.
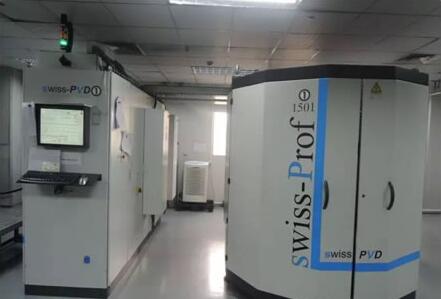
In recent years, domestic manufacturers have been committed to the development and production of AlCrN coatings, using the advanced coating equipment provided by Swiss-PVD, and the very mature AlCrN coating process independently developed to produce the best AlCrN coating on the market. The AlCrN coating is blue-gray, with a maximum temperature of 1100, a friction coefficient of 0.3, a nanohardness of 3300 HV and a film thickness of 0.4-4. Suitable for the processing of hobbing cutters, punching bars, stamping dies, knives and high-gloss stainless steel.
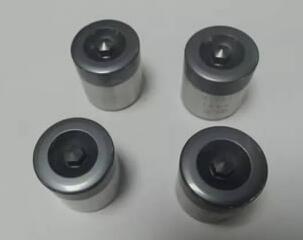
At present, domestic manufacturers are actively working with Swiss OEMs to develop a quaternary Cr-based coating with some X trace elements. In fact, the applicable temperature is above 1100. The adhesion between the coating and the substrate is excellent, and it has better thermosetting and heat insulation. Properties, cutting edge stability, anti-adhesiveness and chip removal, can effectively reduce the cutting force, the overall performance is superior to other brands of AlCrN coating, making it more suitable for hard cutting, high temperature, high cutting force (to the cutting edge) Such extreme environments (milling, drilling, fine tool finishing, etc. of high hardness hardened steel) can be used for tools such as ball knives, end mills, and knives. Compared with the common coatings of the same application (AlTIN, etc.) on the market, the life expectancy is nearly doubled.
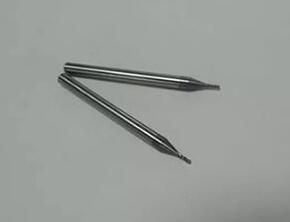
Roofing Steel Corrugated Sheet,Zinc Coated Sigma Post,Galvanized Sigma Posts
Shandong Hengfeng Group , https://www.luhengfeng.com